Composite hulls: stronger, lighter, tougher
There are two material types used for constructing ice-water airboat hulls: composite and aluminum. Due to its strength and durability, composite hulls are used in constructing all of 1000 Island’s airboats.
A composite hull is:
-
Created by bonding individual fibers together
-
Easily flexes without cracking
-
Designed in a V bow that more easily transitions back onto ice
An aluminum hull is:
-
Created by welding individual metal pieces together
-
Cracks after flexing just a few times
-
Designed in a flat bottom and punt nose that makes maneuvering difficult
Composite/fiberglass airboat hull
A composite hull is often called a fiberglass hull. However, “fiberglass” is a somewhat misleading term, as it describes just one component of a composite material. The other component is a plastic vinyl ester, and sometimes epoxy as well. A more accurate term for composite is fiberglass-reinforced plastic (FRP) or glass-reinforced plastic (GRP).
How composite hulls are created
The principle is simple: a binding medium stiffens and strengthens a very strong fibrous material. For example, if you mix concrete and steel together, your structure is more powerful than if it’s just concrete or just steel. The sum is much stronger than its parts.
For a fiberglass airboat, the medium is the resin. The stiffening fibers are spun glass and graphite filaments, which are ten times thinner than a single human hair and much lighter than concrete or steel.
Individually, these fine glass fibers are extremely strong. When held together by plastic resin, they form super tough, rigid, light shapes that can handle flexing and are easy to work with. They can be casted into almost any shape, which is a huge advantage for an ice-water boat hull design.
The resin begins as a liquid and solidifies after a catalyst or hardener is added to it. This is a chemical reaction that cannot be undone. Thermosetting plastics like polyester, vinyl ester and epoxy become permanently solid after setting. They are light, super strong, tougher than aluminum, stand up to flexing and can be easily and cost-effectively repaired.
On the other hand, an aluminum airboat hull gets brittle when cold, breaks next to its welds after flexing just a few times and takes skilled craftsmen, special welders and a proper environment to repair or modify.
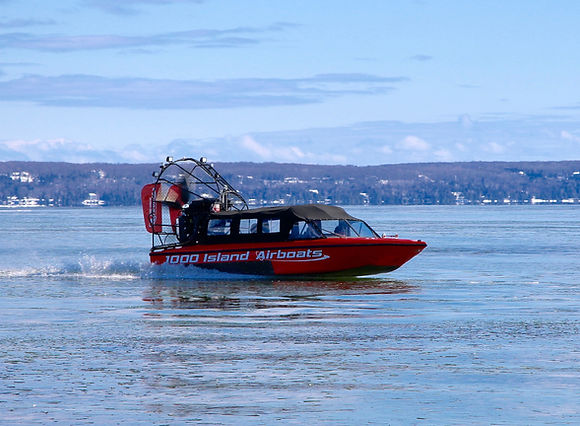.jpg)
How aluminum hulls are created
To construct an aluminum airboat hull, flat panels of aluminum are cut to spec and welded together. It’s a misconception that aluminum is lighter and stronger than composite. Pound for pound, composites are stronger and have higher impact resistance than aluminum.
Ice-water airboats need to be resistant to point loading. Aluminum ice-water airboats have to be made from a heavy gauge aluminum sheet and require reinforcing to try to resist puncture and stop flexing.
Aluminum hulls are heavier than composite hulls
Size for size, an aluminum ice-water rescue boat can weigh 1.5 to 2 times more than a composite boat. Aluminum hulls also last as short as one season before hull maintenance becomes an issue.
A big weight disadvantage of aluminum-built airboats with flat bottoms is drag. This increases the dangers of ice/water transitions. Flat bottom airboats are also so heavy they can’t climb over pressure ridges (an ice ridge produced when floating ice buckles or crushes against each other).
Another concern is metal fatigue when operating on solid ice in subzero temperatures.
Aluminum flat bottom airboats are much less maneuverable, require more power and tend to “snowplow” (piling up wet snow in front), further adding to performance and safety issues. During rescue, this snowplow effect can crush anyone in broken ice.
Composite and aluminum hull comparison
Stress
1000 Island Airboats Composite Hull
Composite hulls are more flexible and much less susceptible to damage caused by uneven ice battering. As the airboat travels at high speed over uneven ice, the composite hull will give rather than crack or break. Also, because there is no seam, the composite hull doesn’t have any weak joints that may come apart.
Aluminum Construction
In cold weather, aluminum hulls don’t handle stress nearly as well as composite hulls. The constant battering of the aluminum hull creates cracks when the air is cold. While these cracks can be repaired by welding, the problem is that the weld is stronger than the aluminum. That means there is variance in hull strength. As the boat is then driven over ice and again subjected to battering, the weaker aluminum flexes with the stronger weld and hull integrity is compromised.
Repair
1000 Island Airboats Composite Hull
Composite hulls from 1000 Island Airboats are easily repairable. In fact, any person with a limited skillset can repair damage with a repair kit and a few simple tools. A more important feature, however, is that after repair, the hull is returned to 100% structural strength.
Aluminum Construction
Aluminum hulls are more difficult to repair. You must have power, a good environment and a skilled welder.
Maneuverability
1000 Island Airboats Composite Hull
The V shape hull creates a “pivot point” that allows turning under much less power. And allows the boat to easily turn out of the channel and climb back on the ice.
Aluminum Construction
The square hull on aluminum boats doesn’t turn easily. This is an even bigger problem if the boat happens to break through the ice and a “channel” is created with ice on both sides and water under the hull. Because of its flat design, the aluminum hull becomes “stuck” in the channel, whereas the V shape composite hull can easily turn out of the channel and climb back on the ice.
Drag
1000 Island Airboats Composite Hull
V hull design means less drag, easier handling and less power required for more speed
Aluminum Construction
The drag created by flat hull design means less speed and sluggish handling.
Bow Design
1000 Island Airboats Composite Hull
The V bow “cuts” through even the most difficult ice-water conditions, allowing the airboat to easily travel through any water, ice, snow and slush.
Aluminum Construction
The punt nose bow design on aluminum airboats creates a “snowplow” effect when travelling over ice. This effect is even more pronounced over slush and snow. There have been occasions where, because of the punt nose design, aluminum airboats operating in heavy snow and slush became bogged down and totally inoperable.
Enclosed Cockpit
1000 Island Airboats Composite Hull
The composite design includes a fully enclosed cockpit and stern, which prevents any water from collecting in the hull.
Aluminum Construction
Aluminum airboats are either completely open or only have an enclosed cockpit. One of the dangers of this design is that there have been cases where airboats in very uneven ice terrain have slid back and filled with water.
Structural Integrity
1000 Island Airboats Composite Hull
1000 Island Airboats are constructed using unique molds. That means our airboats don’t have seams. They’re one piece, with 100% structural integrity from bow to stern. For increased strength, our airboats are also designed with six stringers.
Aluminum Construction
Because aluminum airboats are designed with several pieces of material welded together, there could be weaknesses in the seams.
Polymer Panels
1000 Island Airboats Composite Hull
There is a vast difference in the way the polymer panels are added to aluminum hulls and 1000 Island Airboat hulls: 1000 Island Airboats has “steps” built into the design to accommodate recessing of the polymer panels on the sides and bottom of each boat. This means that there is no edge drag on the polymer panel.
Aluminum Construction
Polymer panels on aluminum airboats are simply add-ons, with no step or recess in the hull to accommodate the panel. The result is tremendous friction built up on the panel. The panel can become distressed or even peel away from the hull.
Floatation
1000 Island Airboats Composite Hull
1000 Island Airboats have floatation built into the hull. The floatation is married to the hull and cannot be dislodged.
Aluminum Construction
Aluminum airboats have floatation strapped onto the hull. There have been documented cases of the floatation apparatus becoming dislodged.
If you want to download the above comparisons, a PDF is available here.
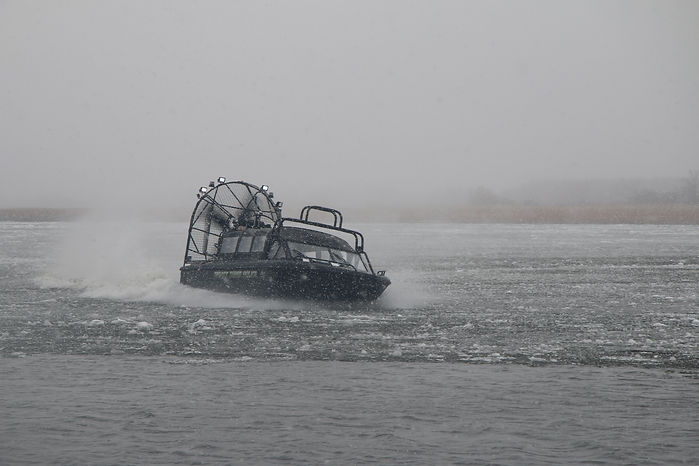
“I'm not sure about all the USCG airboats. I know they've used several different manufacturers over the last few years, trying to find one that'll hold up to their mission profiles on the Great Lakes. From what I hear from USCG, they're destroying the boats after one season, while destroying the structure inside. Extreme vibration and shock, stress and extended operations is wreaking havoc on welds.”
- An aluminum airboat industry expert